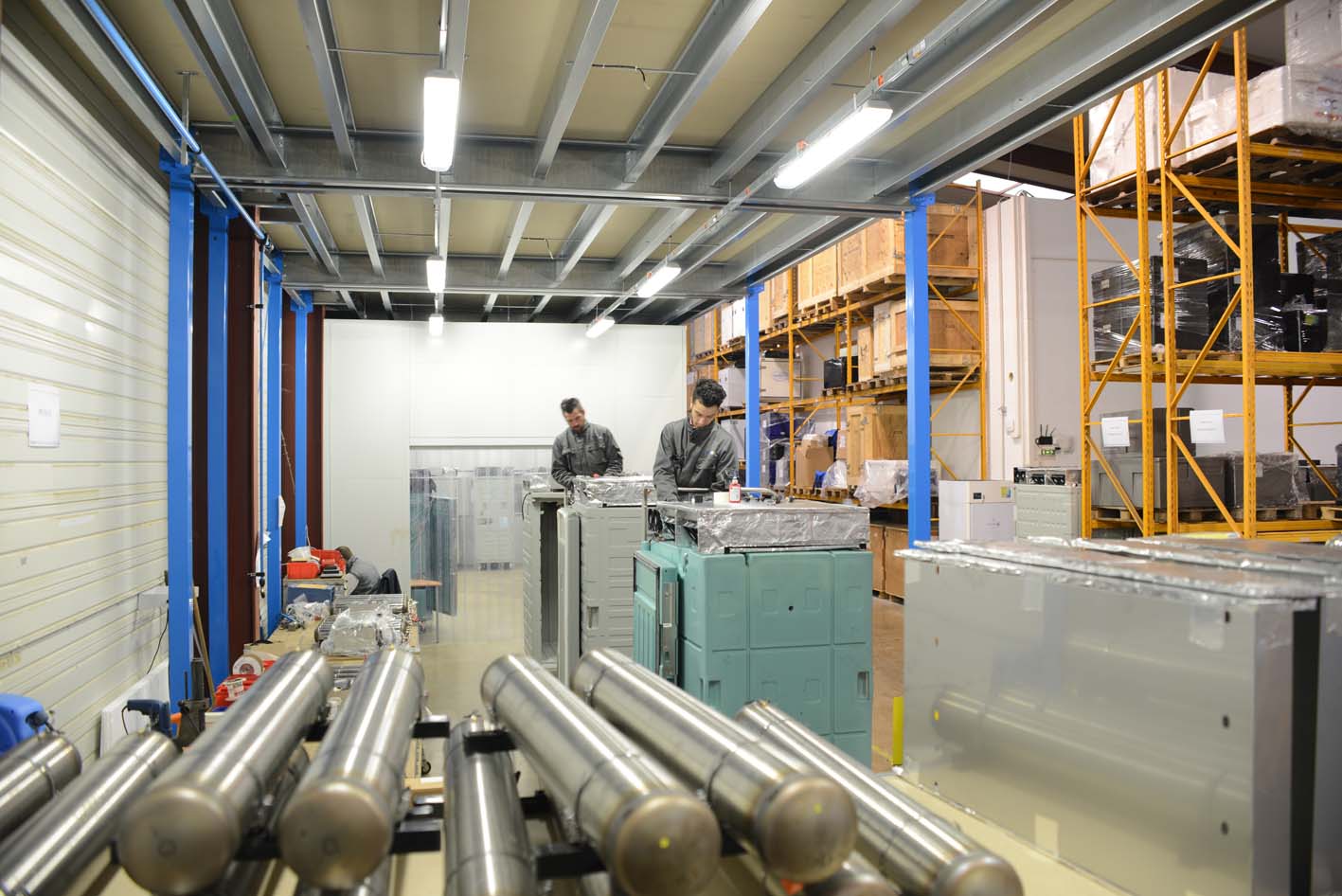
Thermochemical conversion of municipal solid waste into energy and hydrogen
The rising global population is inducing a fast increase in the amount of municipal waste and, in turn, issues of rising cost and environmental pollution. Therefore, alternative treatments such as waste-to-energy should be developed in the context of the circular economy. Here, we review the conversion of municipal solid waste into energy using thermochemical methods such as gasification, combustion, pyrolysis and torrefaction. Energy yield depends on operating conditions and feedstock composition. For instance, torrefaction of municipal waste at 200 °C generates a heating value of 33.01 MJ/kg, while the co-pyrolysis of cereals and peanut waste yields a heating value of 31.44 MJ/kg at 540 °C. Gasification at 800 °C shows higher carbon conversion for plastics, of 94.48%, than for waste wood and grass pellets, of 70–75%. Integrating two or more thermochemical treatments is actually gaining high momentum due to higher energy yield. We also review reforming catalysts to enhance dihydrogen production, such as nickel on support materials such as CaTiO3, SrTiO3, BaTiO3, Al2O3, TiO3, MgO, ZrO2. Techno-economic analysis, sensitivity analysis and life cycle assessment are discussed.
Population growth at a greater pace, rapid urbanization, higher living standards and sophisticated lifestyle have a very large impact on consumption patterns and the generation of wastes. Industrial and domestic activities generate waste which may be degradable or non-degradable, hazardous or non-hazardous to the surrounding environment and cause adverse health effects on the living beings. Waste materials can be either in solid or in liquid forms and fall under different categories such as municipal solid wastes, industrial wastes, medical wastes, radioactive wastes, chemical wastes and agricultural waste.
The management of wastes is very important to reduce the adverse effect on the environment. Statistics say that the annual growth rate of municipal solid waste ranges from 3.2 to 4.5% in developed countries and 2–3% in developing countries.The emanation of waste in solid forms is of very large proportion and highly complex to handle. The municipal solid waste generation report from the United Nations affirms that almost 100% of the goods procured by consumers get converted to waste in a span of 6 months
Though the recyclable waste proportion is estimated closer to 80%, about 90 to 95% of the wastes reaches the landfills due to improper handling and the disposal of them .All developing countries are facing challenges in collecting and disposing the waste. In many countries, food wastes and plastics are the major contributors of municipal solid wastes.Furthermore, due to the outbreak of coronavirus disease followed by sudden lockdown across the world, the drastic increase in the usage of plastic materials, i.e., face mask and gloves, has increased the municipal solid waste generation rate with approximately more than 6000 tons per day in Southeast Asian countries.
A few decades ago, waste-to-energy technologies were introduced to produce energy and valuable products from waste and paved way for finding technologies in processing wastes based on a tool called ‘waste hierarchy’—reduce, reuse, recycle and recover to landfill.The aim of waste hierarchy is to reduce the waste generation and to increase the recycle and reuse of the waste materials. Waste hierarchy method helps in reducing greenhouse gas and pollutants which harm the environment.The paper and plastic are the major fraction in municipal solid waste ranging from 50 to 80% while the remaining fraction is contributed by textile, wood, sewage waste, kitchen wastes and laundry waste. The composition of municipal solid waste may vary depending on local economy, climatic condition, lifestyle and infrastructure. The waste generation of an area is proportional to the average income of the people. Demolition and construction activities consist of used wood and may contain 2–3% of non-wood such as glass, plastics, concrete and scrap metals.
The annual quantity of solid wastes generated in India has increased from 6 million tons in 1947 to 48 million tons in 1997 and to 90 million tons in 2009 and also expected to increase by 2047 up to 300 million tons .The management of municipal solid waste is commonly reduced by incineration, about mass reduction (70–80%) and volume reduction (80–90%) and utilized as electricity with net electrical efficiency of 30%.Plastic materials possess certain intrinsic properties similar to fuels which makes them as a throughput material for the production of heat, steam and several other fuels through thermochemical methods. In addition, biomass from different sources can be used as renewable sources for energy production. During thermochemical treatments when compared to fossil fuels, biomass emits a reduced amount of SOx, NOx and greenhouse gases.The waste-to-energy is one of the most promising alternative methods in waste management strategies.
About 80% of energy is derived from petroleum products to satisfy the energy demand around the world. The thermochemical treatment of municipal waste is gaining momentum as the most promising waste-to-energy production method mainly due to sustainability. The studies showed that less than 100,000 m2 of land is enough to treat 1 metric ton per year of waste for 30 years, while 3,000,000 m2 is necessary for landfilling of 30 metric tons of municipal solid waste .The concentration of organic and inorganic contaminant can be securely disposed and utilized by thermochemical treatment without any threats.
The by-products obtained from thermochemical methods such as bottom ash, solid residues and metal or non-metal slags are recyclable and can be reused. The emission of greenhouse gas and other pollutants are significantly minimized and estimated that about one ton of CO2 is retrieved when compared to landfilling. Life cycle assessment studies considered that waste-to-energy technology has a less impact on the environment and can be used as a source for power generation. The electricity and process heat from thermochemical treatment methods can be utilized for both industrial facilities and for residential or commercial power requirements.
Thermochemical conversion technologies
Biomass is a renewable, clean and green source to produce fuels that can cater the energy needs. However, the direct usage of biomass as biofuels has many limitations such as poor calorific value, undesirable moisture content, abnormal composition and properties. Thermochemical techniques offer pathways that alleviate these disadvantages and drastically reduce the undesired by-products by optimizing the operating conditions.Combustion, gasification, pyrolysis, hydrothermal carbonization and torrefaction are the thermochemical methods that aid in the production of biofuels from lignocellulosic and non-lignocellulosic materials. shows an outlay on various thermochemical treatments of municipal solid waste for biofuel production and reforming processes.
Torrefaction into solid products
Biomass can be converted into char, coke and biochar which have similar properties to that of coal. Biochar derived from torrefaction possesses properties of coal fuel. Torrefaction is the mild pyrolysis process carried out in the absence of oxygen or in an inert atmosphere at 200–300 °C to produce biofuel with improved fuel characteristics; the torrefied solid biomass has high calorific value, low moisture content and other properties such as grindability and hydrophobicity.. The aim of torrefaction is to produce solid fuel as an alternative to coal and to produce materials with high hydrophobicity.
The toasted biomass contains much volatile matter and requires high residence time to reduce the volatile matter. Combustion reactions are suppressed because of low oxygen supply. Improved grindability reduces power cost required for size reduction and enables the displacement of coal usage. Additionally, the lower equilibrium moisture content of the torrefied biomass has the advantages of storage ease and higher heating value .Gaseous products produced in the torrefaction process are classified into permanent gas (CO and CO2) and condensable gas (acetic acid and water). Torrefaction is also reported as a thermal pre-treatment process of biochar production to improve the energy density and used as a low-moisture feedstock to produce energy. Torrefaction may be light, mild or severe based on the temperature input required to consume the lignocellulosic contents of the biomass. In torrefaction process products can be in all three forms and most of those can be used as fuels. Some of the products received in torrefaction are H2, CO2, toluene and benzene (gaseous form); H2O, acetic acids, alcohols, aldehydes and ketones (liquid form); and char and ash (solid form).
Pyrolysis to produce liquids
Biomass can be converted into liquid fuels, namely, bio-oil, bio-diesel and bio-ethanol by using pyrolysis, transesterification and fermentation, respectively. The scope of this review is limited to production of bio-oil through pyrolysis as the other methods are non-thermochemical techniques. In pyrolysis technology waste materials are degraded thermally with restricted supply of air or oxygen at 300–600 °C to generate the energy in the form of fuel, biochar, syngas and biofuel precursors. Pyrolysis is an irreversible process; the materials which undergo the process are continuously subjected to changes in physical and chemical composition.
The pyrolysis process has a wide range of applications in chemical industries for the production of methanol, biochar and activated charcoal with the only limitation being emission of harmful gases which causes adverse effects in the environment. The biochar produced through pyrolysis assists in adsorption and used in heavy metal remediation, soil amelioration and carbon sequestration. The biochar is also used as a soil conditioner which can alleviate about 0.75 gigatons of carbon or 2.75 gigatons of carbon dioxide per year if used globally on an average till 2050 .
The fuel product of pyrolysis, called as pyrolytic oil (dark brown color liquid) is characterized by large water and oxygen content, high acidity with pH from 2 to 4, low vapor pressure, high viscosity, weak stability and low heating value (16–19 MJ/Kg). The bonds in hydrocarbons are thermally broken to produce bio-oil at the temperature range of 400–800 °C. Pyrolysis can be slow, fast, catalytic or microwave-assisted. The main products in the slow and fast pyrolysis process are biochar and bio-oil, respectively, where slow pyrolysis incurs low heating with long residence time and fast pyrolysis incurs high heating with short residence time .
Bio-oil contains more than 300 organic compounds; however, bio-oil is not directly used as a fuel due to several disadvantages. The by-products generated through the bio-oil production depend on temperature, particle size, heating time, catalyst used and heating rate. High-quality bio-oil can be produced by using noble metal-supported catalysts and further processing in refineries.
Comments 0