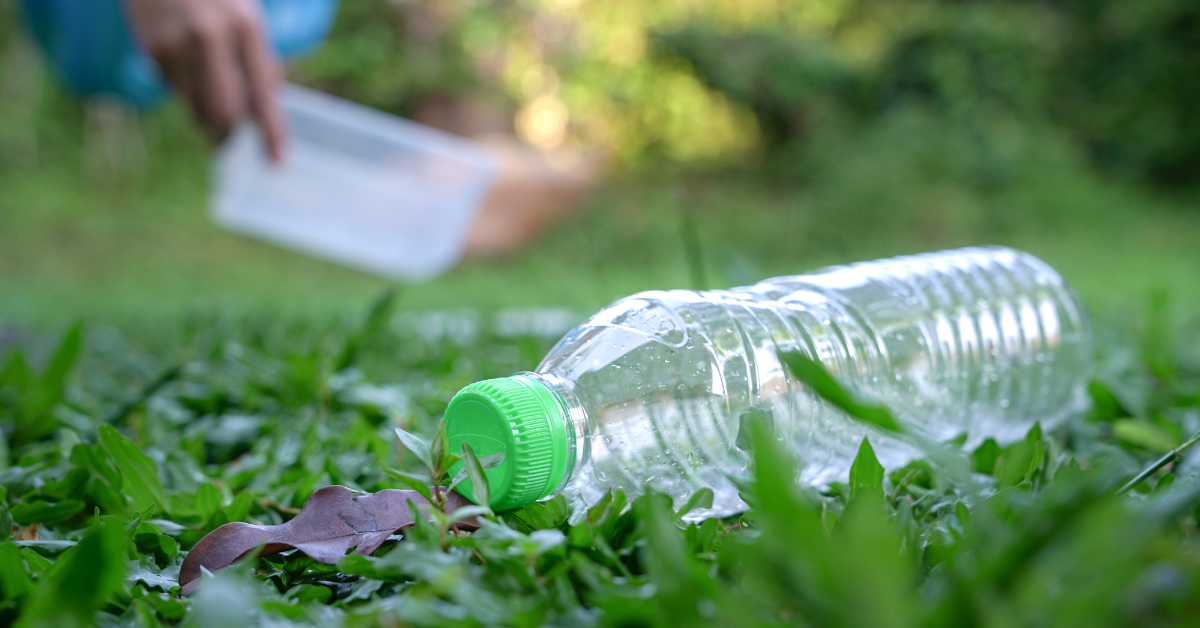
Thermochemical Recycling: Advancing the Circular Plastics Economy
Thermochemical recycling is emerging as a crucial complement to mechanical recycling, offering innovative solutions for the processing of complex plastic waste streams. This advanced recycling method plays a significant role in the circular economy, addressing challenges posed by mixed and hard-to-recycle plastics
Pyrolysis and Direct Steam Cracking
Pyrolysis stands out as a versatile thermochemical process capable of handling various plastic waste types. It can produce a wide range of products for the chemical and plastics industry, realising both open and closed recycling loops.While many players focus on large-scale pyrolysis plants using highly sorted municipal plastic waste, there's growing interest in small-scale, decentralised facilities suited for processing low-quantity waste streams, including industrial residues and hard-to-recycle plastics.Direct steam cracking offers another innovative approach to handling heterogeneous plastic waste. A fluid bed reactor can be used for direct steam cracking to process a wide variety of polymer-rich wastes, operating at temperatures similar to traditional naphtha crackers (750-850°C). These processes can even handle uncleaned food packaging and reject fractions from mechanical recycling, producing a product stream comparable to naphtha cracker effluent.
Industry Perspectives and Challenges
The development of thermochemical recycling technologies involves various stakeholders, including chemical companies, refineries, waste management firms, and EPC contractors. A key question in the industry is whether advanced plastic recycling will be located close to plastic waste sources and/or around steam crackers.Experienced EPC contractors play a crucial role in scaling up these technologies, addressing safety concerns, material selection, and design issues that arise during plant scale-up.
Environmental and Economic Considerations
While thermochemical recycling offers promising solutions for hard-to-recycle plastics, it's important to consider its environmental impact. Blueplasma Power's Gasification technology, for instance, claims to produce high-value outputs with an 80% lower CO2 footprint compared to traditional methods. Economically, the viability of Pyrolysis depends on factors such as oil prices, recycled plastic demand, and regulatory incentives. Small-scale pyrolysis plants are being evaluated for their economic potential in handling low-quantity waste streams.
Conclusion
Thermochemical recycling technologies are rapidly evolving, offering promising solutions for the plastic waste crisis. As these technologies mature and scale, they have the potential to significantly contribute to a more circular and sustainable plastics economy. However, continued research, development, and policy support will be crucial to overcome remaining challenges and fully realise the potential of thermochemical recycling.
Comments 0